Processing Setup
At Phillips 66, we recognize the competitive advantage of delivering polypropylene pellets with superior quality. To that end, we continuously optimize our Quality System to capitalize on the innovation of our people and ensure our business strategies and operational processes are implemented successfully,
Our customers can trust our trademark quality of our products and services. We value your business and thank you for partnership.
Sheet Extrusion & In-Line Thermoforming Process
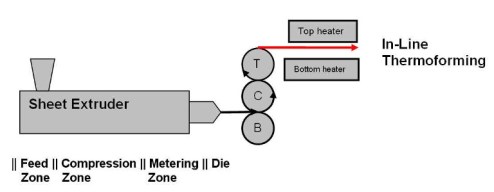
First certified in 2006, our Quality System meets the scrutinizing criteria of ISO 9001:2008 standards. Our Quality System focuses on implementing our business strategies and operational plans with excellence. We continue to successfully reach our quality targets while consistently delivering reliable products and services to our customers. We believe that through Quality comes Success, and we want that to be your experience too. We welcome your questions and value your feedback.
processing parameter | typical settings* |
---|---|
Barrel: Feed Zone | 400–420 °F |
Barrel: Compression | 410–430 °F |
Barrel: Metering Zone | 430–450 °F |
Adapter and Screen Changer | 430–440 °F |
Die Temperature | 450–480 °F |
Melt Temperature | 440–475 °F |
Chill Rolls: Top (T) | 150–160 °F |
Chill Rolls: Center (C) | 160–175 °F |
Chill Rolls: Bottom (B) | 140–150 °F |
Thermoforming: Top Heater | 400–430 °F |
Thermoforming: Bottom Heater | 400–435 °F |
Thermoforming: Forming Temperature | 300–310 °F |
Injection Process
injection molding parameter | typical settings |
---|---|
Melt Temperature: Nozzle | 450–460 °F |
Melt Temperature: Adapter | 440–450 °F |
Melt Temperature: Front | 450–470 °F |
Melt Temperature: Middle | 440–460 °F |
Melt Temperature: Rear | 430–450 °F |
Hot Runner / Manifold Temperature | 380–420 °F |
First or Boost Stage Injection: Time | 5–10 sec (less for smaller parts) |
First or Boost Stage Injection: Pressure | 1,200–2,000 (max) psi |
Fill Speed: First 10% of Shot | 1.5 in/sec |
Fill Speed: Next 70% of Shot | 2.3 in/sec |
Fill Speed: Last 20% of Shot | 1.2 in/sec |
Packing Stage Time | 4–8 sec |
Second or Hold Stage Injection: Time (with a packing stage) | 6–11 sec |
Second or Hold Stage Injection: Time (without a packing stage) | 9–15 sec |
Second or Hold Stage Injection: Pressure | 60% of max inj. pressure psi |
Cushion | 0.25–0.50 in (dependent on shot size) |
Screw Speed | 60–100 rpm |
Back Pressure | 50–200 psi |
Mold Temperature | 70–120 °F (actual surface pyrometer reading) |
Clamp Pressure | 2.2(A) tons/in2 |
Drying Conditions | usually not required |
Purging | Polyethylene (PE), polypropylene (PP) or standard purging compound |
2.2 TONS/IN2 OF PROJECTED MOLD AREA. THIS IS DEPENDENT ON WALL THICKNESS, FLOW DISTANCE AND FLOW DIRECTION CHANGES.
Before using this product, the user is advised and cautioned to make its own determination and assessment of the safety and suitability of the product for the specific use in question and is further advised against relying on the information contained herein as it may relate to any specific use or application. It is the ultimate responsibility of the user to ensure that the product is suited and the information is applicable to the user’s specific application.
Phillips 66 Company does not make, and expressly disclaims, all warranties, including warranties of merchantability or fitness for a particular purpose, regardless of whether oral or written, express or implied, or allegedly arising from any usage of any trade or from any course of dealing in connection with the use of the information contained herein or the product itself. The user expressly assumes all risk and liability, whether based in contract, tort or otherwise, in connection with the use of the information contained herein or the product itself. Further, information contained herein is given without reverence to any intellectual property issues, as well as federal, state or local laws which may be encountered in the use thereof. Such questions should be investigated by the user.